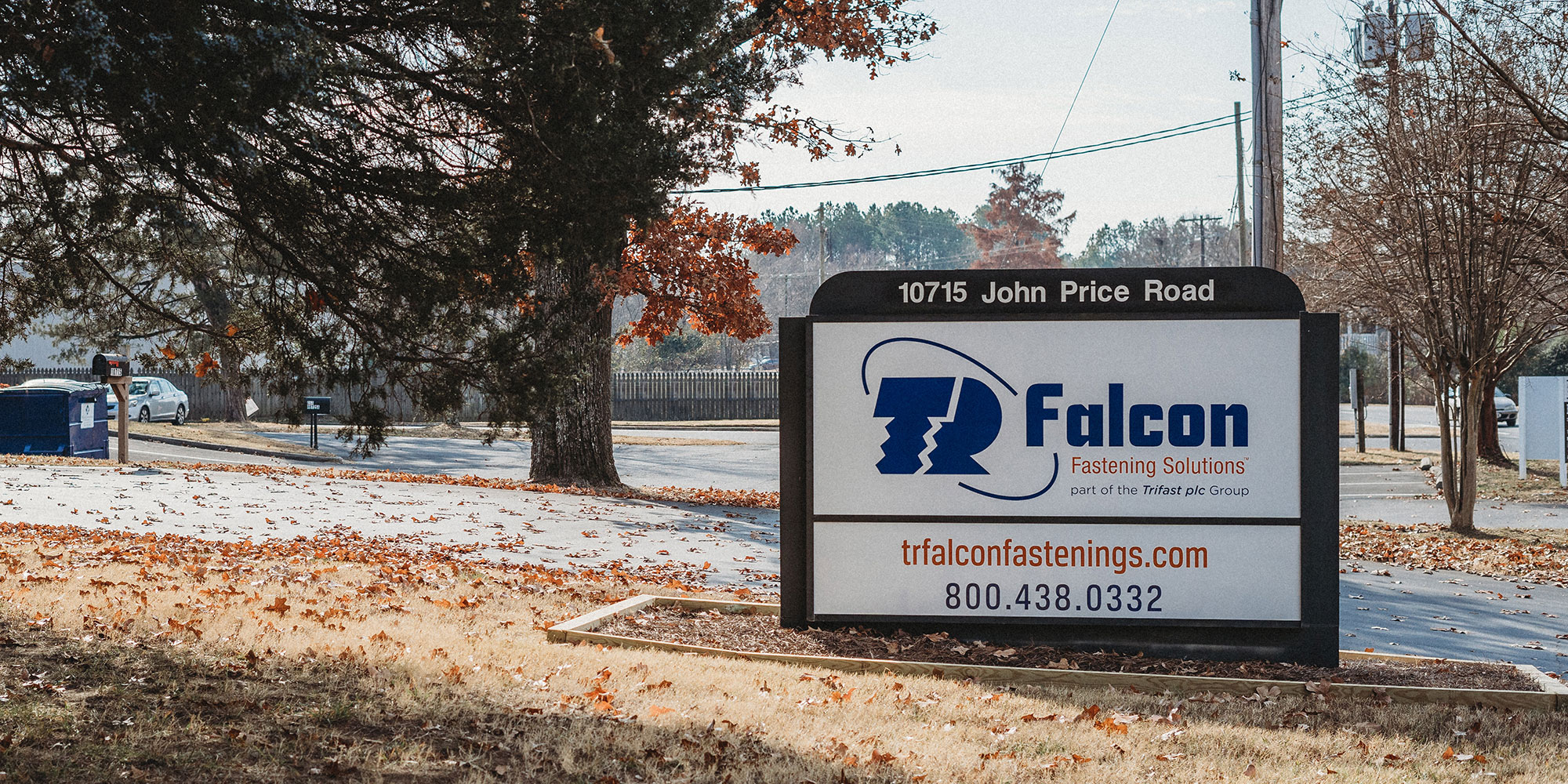
Fastener supply & inventory management
TR Falcon Fastening Solutions, Inc., part of the Trifast plc group, is a distributor of industrial fasteners and other Cat C components and is a specialist in vendor managed inventory (VMI) for original equipment manufacturers (OEMs)
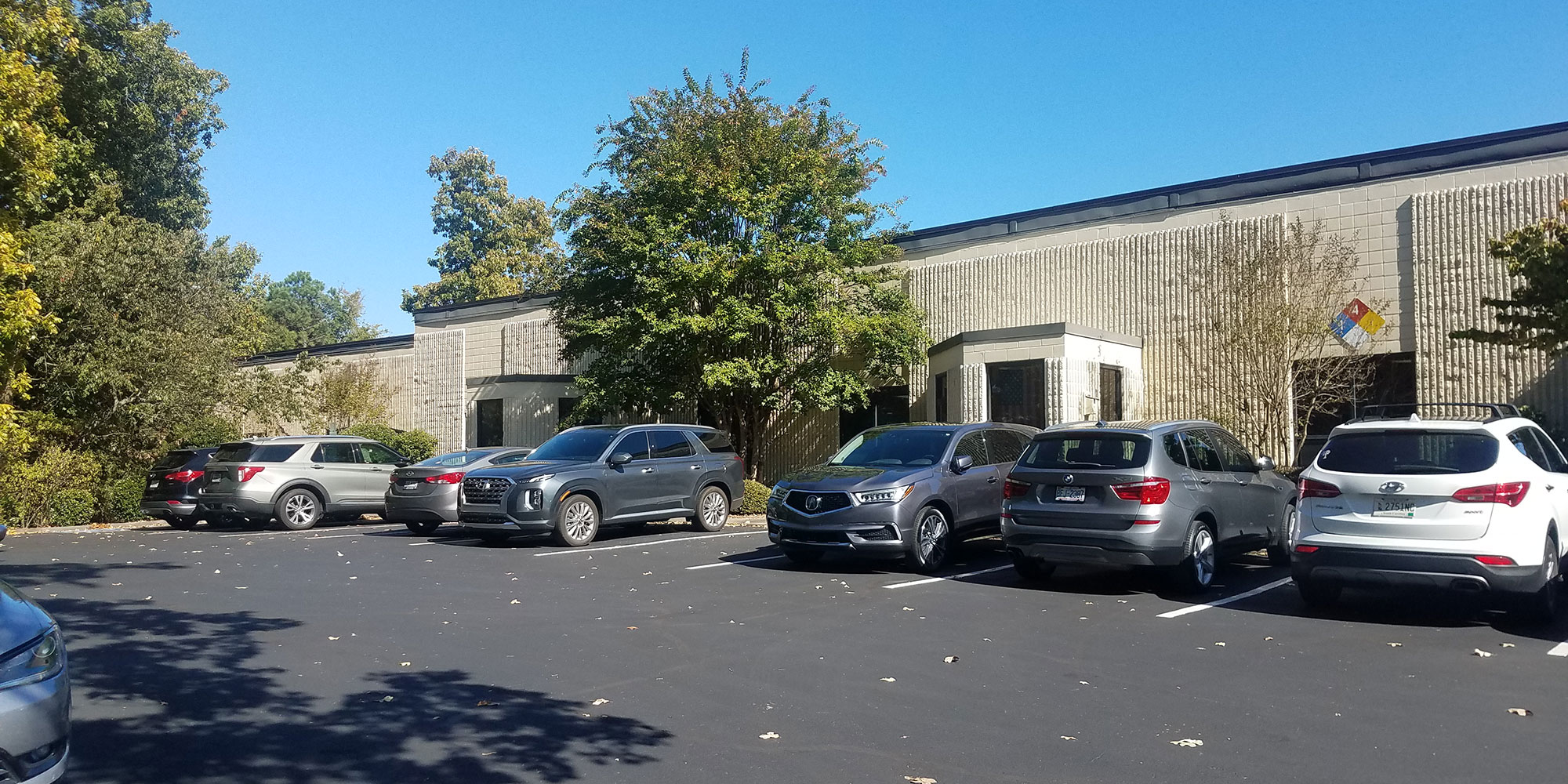
COMPANY
About us
Today, TR Falcon Fastening Solutions has full-service distribution centers in Charlotte NC and Louisville Kentucky with onsite VMI locations in clients facilities in these regions.
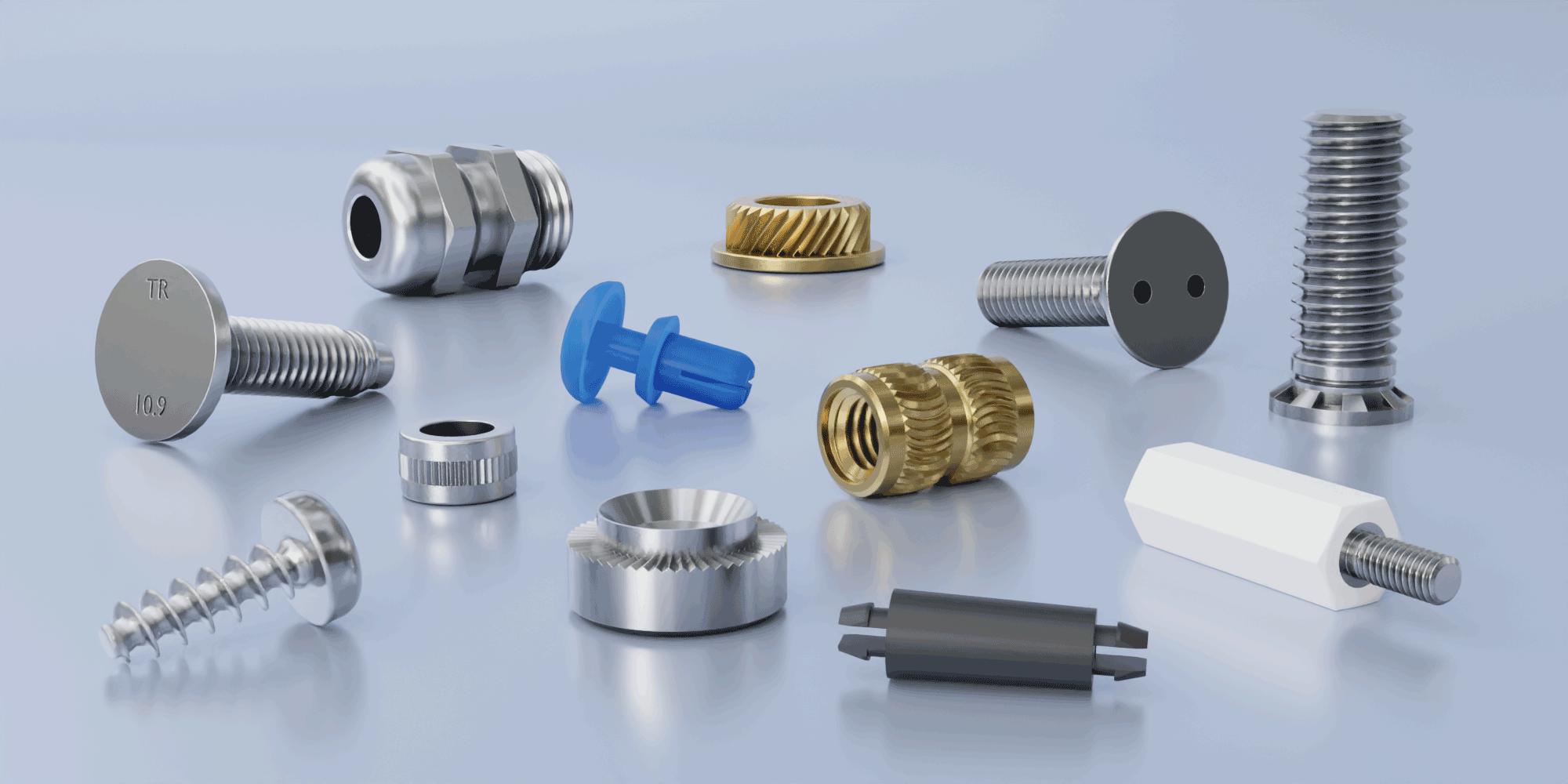
PRODUCTS
Not just fasteners
We have an extensive supply chain capability enabling us to supply a wide variety of fasteners including Class C components you want. Increasingly we are providing kitted product to reduce the total cost of ownership (TCO).
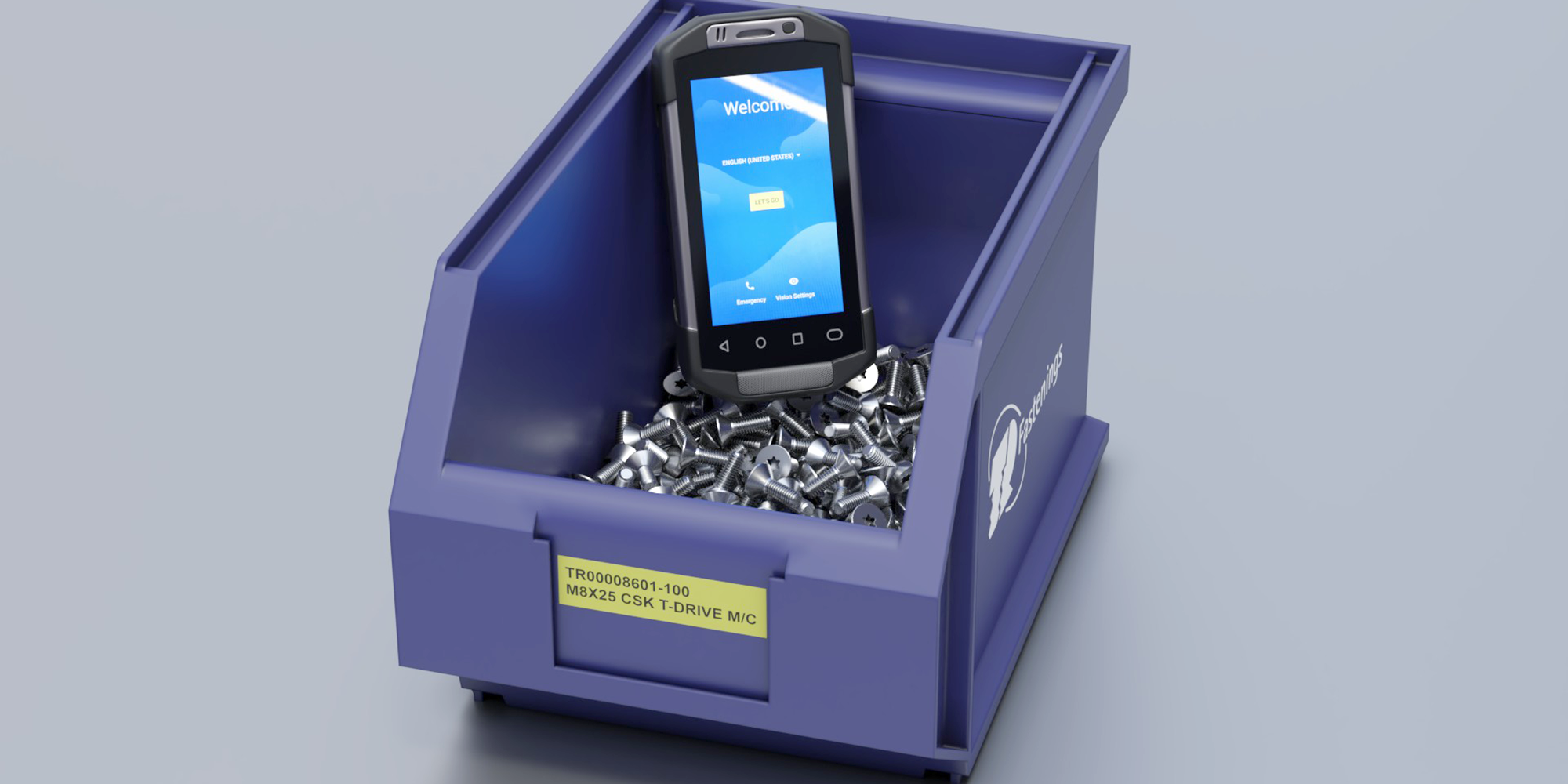
VENDOR MANAGED INVENTORY
VMI programs
Our tailored vendor managed inventory (VMI) programs are bespoke to meet your requirements. We can conduct on site surveys and produce a compatibility report to ensure we meet the brief.
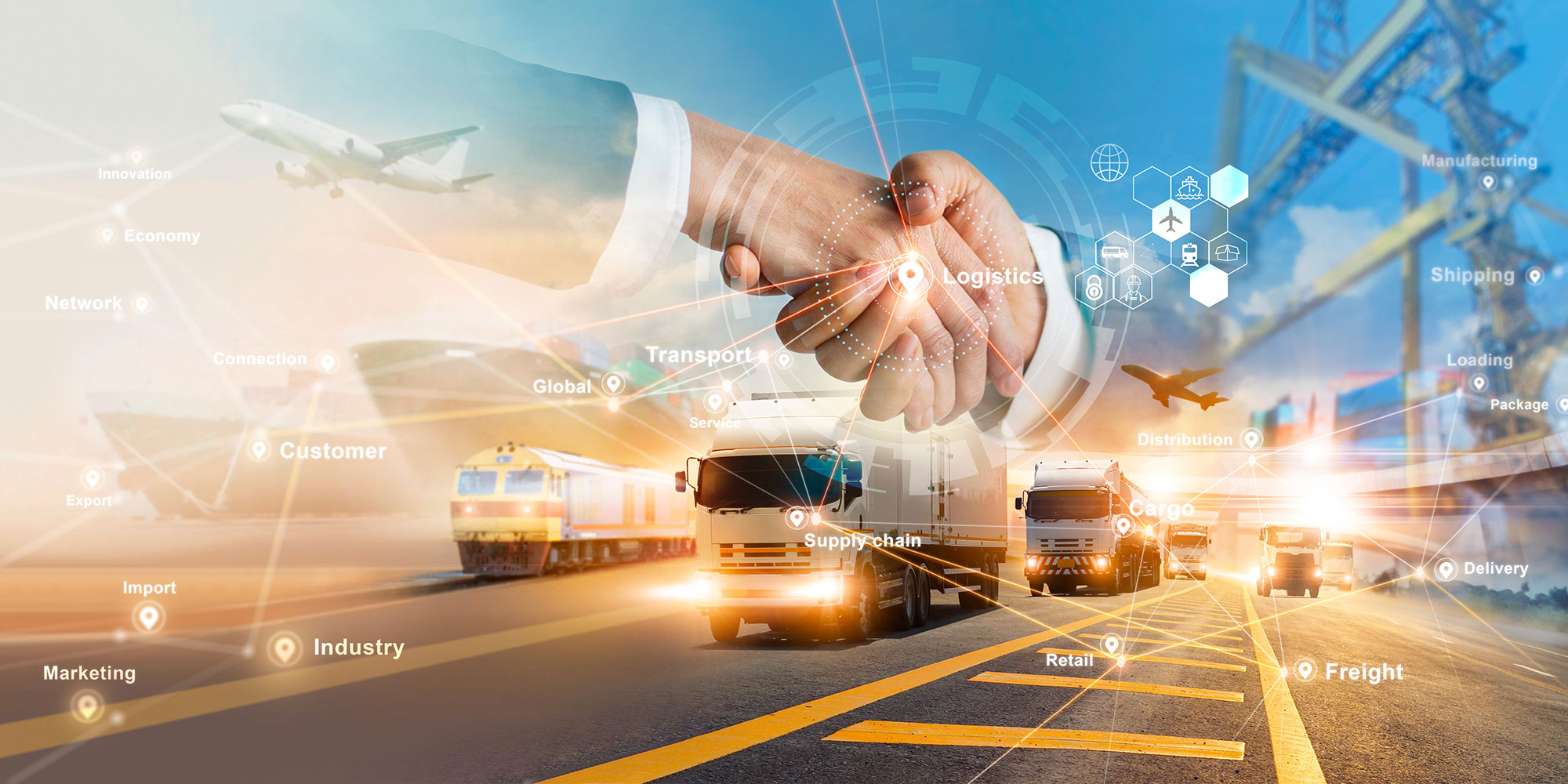
FULL SERVICE PROVIDER
Value-added services
We offer kitting services as well as subassembly in addition to all of our cost reduction services like local delivery, vendor and invoice consolidation and more.
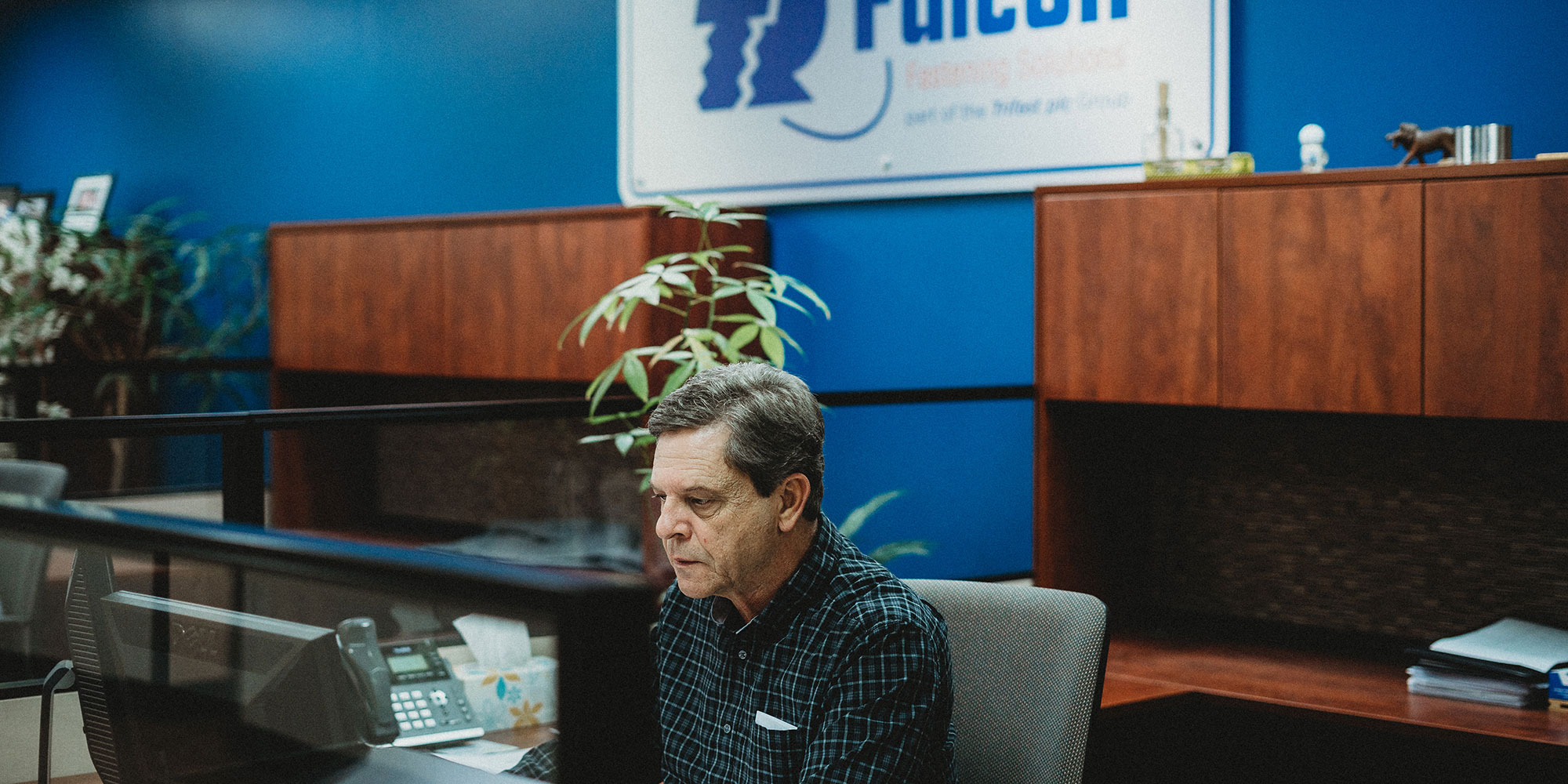
SERVICES
Account management
A dedicated account manager will research your best supply source, manage your inventory levels, and search for cost savings.
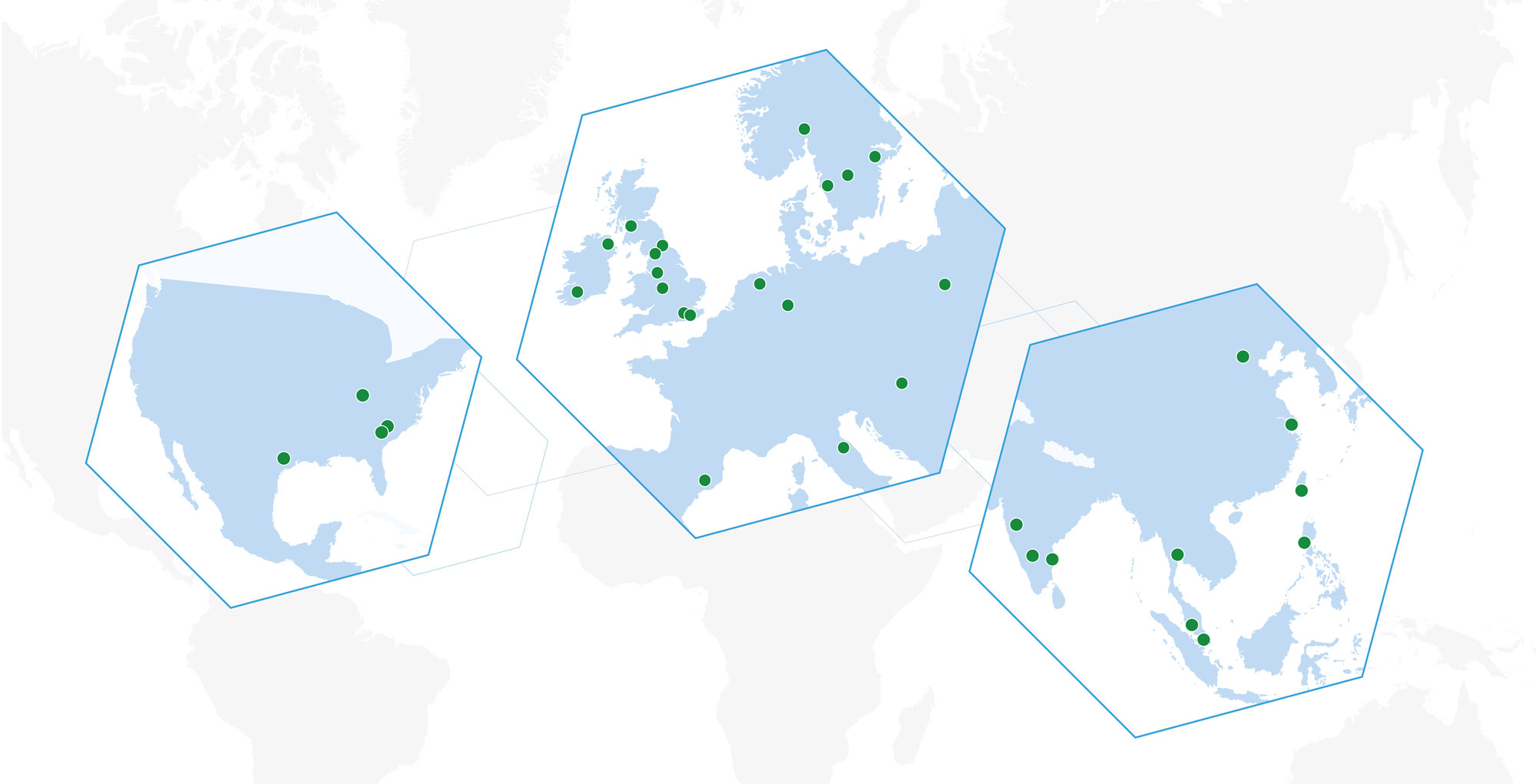
South Carolina
Technical and Innovation Centre
CU-ICAR - One Research Drive, Office 300E, Greenville, SC 29607, USA
Phone: +1 800-280-2181
Email: usa@trfastenings.com
North Carolina
TR Falcon Fastening Solutions
10715 John Price Road, Charlotte, NC 28273
Registered in USA | Registered No: C201409701782
Phone: +1 704-588-4740 or +1 800-438-0332
Email: connect@falconfastening.com
Kentucky
TR Falcon Fastening Solutions
11536 Commonwealth Drive, Louisville, KY 40299
Phone: +1 704-588-4740
Email: connect@falconfastening.com
Latest news
Keep up to date with the latest fastener, industry and Company news from TR and our Group of companies.